Predicted Costs for Retaining Walls in 2025
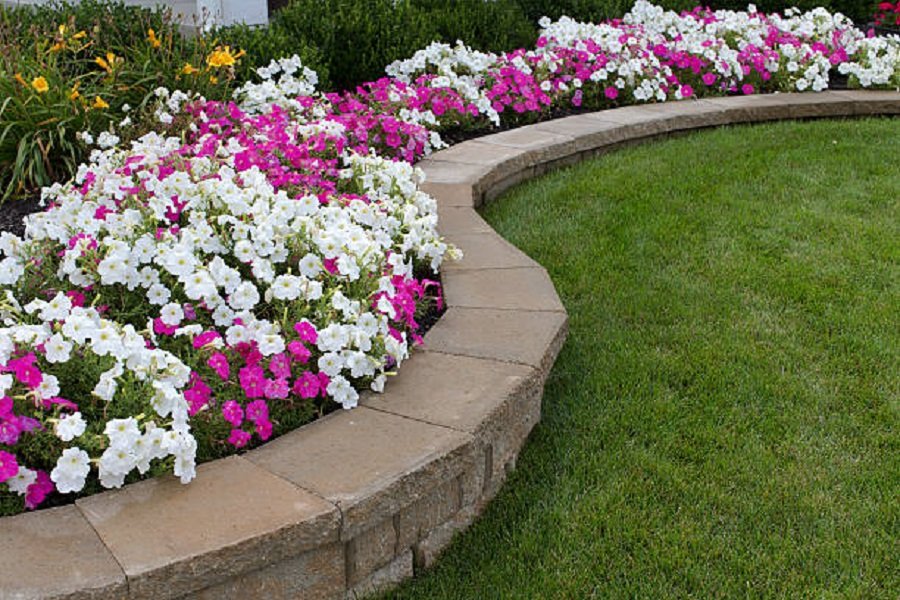
Retaining Walls Costs
As the construction industry continues to evolve, so does the cost of materials and labor associated with building retaining walls. The price of constructing a retaining wall is influenced by numerous factors, including size, materials used, design complexity, and local labor rates.
- Small Retaining Walls (Less than 4 feet): An increase is expected in the current average price of $500-$1500. By 2025, homeowners could be spending between $550 – $1650 on small retaining walls.
- Medium Retaining Walls (Between 4 to 6 feet): The current average cost ranges from $1500 – $3000. By 2025 this might increase to approximately $1650 – $3300.
- Large Retaining Walls (Over 6 feet): These currently cost between $3000 – $8000 on average but by 2025 this could rise to roughly $3300 – $8800.
Please note these estimates could vary based on factors mentioned earlier; material type, design complexity, location, etc.
The projected increases are not only due to inflation but also because of expected advancements in technologies used in constructing retaining walls. This can lead to better-quality structures which might also contribute to higher costs. On top of that, an increase in labor wages is also anticipated which will affect the overall project cost.
In the next sections of this article, we delve deeper into specific aspects affecting retaining wall costs including project size and material types used in construction.
Admittedly, the above costs are only projections. Actual costs could go higher or lower based on market dynamics and economic conditions. But it’s important to prepare early, and these estimates can help property owners start planning their budgets for upcoming projects. Be sure to consult with local contractors and do your own research to get the most accurate estimates for your specific needs.
Detailed Cost Estimations for Retaining Walls Based on Project Size
Retaining walls are a critical element in most landscaping projects. They provide structural stability, prevent soil erosion, and are often a key aesthetic feature. However, their cost can vary significantly based on the size of the project.
Small Project (Less than 25 Square Feet)
- Materials: Interlocking blocks or stones are often used for these smaller projects due to their lower cost and ease of installation. Material costs usually amount to $15-$30 per square foot.
- Labor: The labor cost for smaller projects ranges from $10-$15 per square foot.
Medium Project (25 to 50 Square Feet)
- Materials: For medium-sized retaining walls, concrete blocks or natural stone are popular choices due to their durability and aesthetic appeal. Material costs range from $20-$40 per square foot.
- Labor: Labor costs increase with project size due to complexity and time requirements. Expect labor costs in the range of $15-$30 per square foot.
Large Project (Over 50 Square Feet)
- Materials: Large retaining walls often require reinforced concrete or poured concrete due to load-bearing needs. Material costs may reach upwards of $40 per square foot.
- Labor: Given the technical complexities involved in larger retaining wall projects – including excavation and base preparation – labor costs may reach $30-$50 per square foot.
Keep in mind, these are rough estimates and actual costs can vary based on region, specific material selections, and other project-specific factors. Always obtain multiple estimates and consider all scope parameters before embarking on a retaining wall project.
Despite the costs involved, the value addition to the property from well-constructed retaining walls often outweighs the initial investment. They provide a robust solution for soil erosion issues, enhance outdoor living spaces, and contribute significantly to the overall property aesthetics.
A Breakdown of Retaining Wall Cost by Material Type
When planning a retaining wall project, one of the most crucial elements to consider is the material. The cost can vary significantly depending on the type of material you choose. Let’s delve into a detailed breakdown of retaining wall costs according to material type.
Concrete Retaining Walls
Concrete walls are one of the most commonly used materials for retaining wall construction due to their durability and strength. They are particularly suitable for larger scale projects where stability is paramount. However, they can be on the costly side.
On average, concrete retaining walls cost between $20 and $25 per square foot. This figure includes materials and labor but can increase if additional reinforcement is required or if the design is complex.
Brick Retaining Walls
Brick retaining walls offer a visually appealing option that blends well with traditional architecture. Besides being aesthetically pleasing, they are also highly durable.
The average cost for brick retaining walls ranges from $14 to $15 per square foot, making them a more budget-friendly choice compared to concrete walls.
Stone Retaining Walls
Natural stone walls add an authentic and elegant touch to any landscape design but can be quite expensive due to their high material costs and labor-intensive installation process.
Expect prices in the region of $25 to $40 per square foot for natural stone retaining walls.
Wood Retaining Walls
Wood is a cost-effective choice often used in residential landscaping projects due its affordability and ease of installation. However, wood has shorter longevity compared to other materials like concrete or brick due its susceptibility to decay over time.
Wooden retaining walls typically cost around $15 per square foot depending on the type and quality of wood used.
Corten Steel/Metal Walls
Corten steel, also known as weathering steel, provides an industrial aesthetic that has grown increasingly popular in modern designs. These metal walls are robust and durable with minimal maintenance needs.
The cost of corten steel/metal retaining walls generally falls between $25 and $40 per square foot.
Gabion Retaining Walls
Gabion walls are composed of wire mesh baskets filled with rock or stone. They offer an economical choice due to their simple construction, need for less-technical labor, and use of locally sourced materials.
Costs for gabion retaining walls usually range from $10 to $15 per square foot.
Overall, the material you choose for your retaining wall will play a significant role in determining the overall project costs. By understanding these cost implications, you can plan your budget accordingly and make an informed decision that best suits your needs and preferences.
Exploring the Use of I-Beams in Retaining Wall Construction and its Costs
I-beams, also known as H-beams, W-beams or double-T beams, are an integral part of certain types of retaining wall construction. In particular, these beams are commonly employed in the construction of cantilever retaining walls. They are chosen for their strength and durability, providing vital support to the wall structure. However, their use can significantly influence the overall cost of a retaining wall project.
Generally, I-beam retaining walls comprise a series of vertically placed I-beams embedded into the ground and connected by horizontal sections to form a sturdy wall structure. The I-beams themselves can be made out of steel or wood, but steel is generally preferred for its superior strength and durability.
Cost Implications
- Steel I-Beams: On average, you can expect to pay between $90-$210 per linear foot (including installation) for steel I-beam retaining walls.
- Wooden I-Beams: These tend to be cheaper option comparatively – costing around $60-$150 per linear foot (including installation).
Keep in mind that these costs do not include other materials required for construction like concrete mix for footing or backfill material.
In addition to material costs, labor cost is another significant factor in determining the overall cost of an I-beam retaining wall project. This will vary depending on the complexity of the project, location (labour costs differ across regions), among other factors.
It is also worth considering that while upfront costs may seem high, investing in superior quality materials like steel can lead to longer lifespan and lower maintenance costs over time.
Maintenance Costs
Maintenance costs associated with an I-beam retaining wall may include repair work, paint jobs for protection against rust (for steel beams), or pest control measures (for wooden beams). Generally, steel I-beams require less maintenance than wooden ones and are more resistant to environmental damage.
In summary, while I-beams might increase the initial cost of your retaining wall project, their utilization can provide significant structural benefits. They ensure a strong, durable structure that can last for decades with minimal maintenance. Therefore, when planning a retaining wall construction project, it is necessary to weigh these aspects against the initial investment required.
The Financial Implications of Backfill Methodology in Retaining Wall Construction
Backfilling is an essential part of retaining wall construction, and it involves filling the space behind the wall with material to ensure stability and pressure balance. However, the choice of backfill material and method used significantly impacts the overall project cost. Understanding these financial implications can help you make better budgeting decisions.
Types of Backfill Material
- Natural Soil: This is the most cost-effective option as it re-uses the soil excavated during construction. However, it may lack proper drainage capabilities and could lead to water pressure build-up behind the wall.
- Gravel or Stone: These materials offer superior drainage but come at a higher price point. The additional costs will vary based on local market prices and transportation logistics.
- Engineered Fill: This is a specially designed mixture that combines optimal strength and drainage properties. However, it is usually the most expensive option.
Cost Implications of Different Backfill Materials
The final cost will depend on multiple factors including quantity required, local market prices, and delivery charges.
Consideration of Drainage System Costs
The backfill material’s drainage capability affects the type of drainage system required – another significant cost factor in retaining wall projects. A less expensive backfill material might necessitate a more complex and costly drainage system to prevent water pressure build-up. For example, using natural soil could require installing perforated pipes or weep holes for adequate drainage.
Labor Costs
The type of backfill material used can also affect labor costs. For instance, engineered fill might require less compacting than natural soil, reducing labor hours. However, acquiring and transporting the pricier engineered fill could offset these savings.
Bottom Line
The choice of backfill methodology in retaining wall construction has substantial financial implications that extend beyond the upfront cost of materials. It directly influences other project aspects, such as the required drainage system and labor hours. Therefore, it’s critical to consider all these factors when estimating overall project costs.
When planning a retaining wall project, consult with a qualified engineer or contractor. They can provide accurate cost estimates based on your specific site conditions and project requirements. It will ensure an efficient use of resources without compromising the integrity and longevity of your retaining wall.
The Economic Aspects of Reinforcement in Retaining Wall Projects
Retaining wall projects require a significant investment, and one of the key elements that can highly influence a project’s cost is the reinforcement strategy. Reinforcement not only adds durability to the construction but also improves its overall stability under varying loads. The factors determining the cost of reinforcement include the type of material used, the project’s complexity, and the extent of reinforcement required.
Reinforcement materials can be categorized into three primary types: steel, geosynthetics, and concrete. Each material comes with its distinct price points and benefits.
- Steel: Generally used in large-scale retaining wall projects due to their strength, steel rebars are a common choice for reinforcement. However, they are relatively expensive and may lead to increased project costs.
- Geosynthetics: These are synthetic products used in geotechnical engineering for soil stabilization. Geosynthetics such as geogrids or geotextiles can be highly effective for reinforcing retaining walls but may not be suitable for all soil types and conditions.
- Concrete: Concrete blocks or poured concrete can also serve as reinforcement in retaining walls. While not as strong as steel, concrete offers a balance between strength and cost-effectiveness.
The complexity of a retaining wall project directly impacts the reinforcement requirements – complex projects often need more intensive reinforcement leading to higher costs. Slope steepness, ground conditions, load requirements, height of wall all contribute to the complexity level.
- Higher walls generally require more extensive reinforcement than shorter ones.
- Certain soil types may need more comprehensive support compared to others.
- Walls that must bear heavier loads will require more robust reinforcement compared to those with lower load demands.
These factors cumulatively decide the extent of reinforcement, thus directly impacting the project cost.
Please note these are approximate values and actual costs can vary based on location, supplier, and market fluctuations.
Understanding these economic aspects of reinforcement in retaining wall projects will allow for better budgeting and cost management. It is always recommended to consult with a professional engineer or contractor to get accurate cost estimates tailored to your specific project requirements.
Understanding the Costs Involved with Building a Retaining Wall: A Location-Independent View
Building a retaining wall may be necessary for a variety of reasons, such as supporting soil, preventing erosion, or creating flat terrain on sloping properties. Regardless of the reason, understanding the cost implications is crucial before undertaking such a project. While various local factors can influence the cost, this article will provide a location-independent review of cost considerations to offer general insight.
Material Costs
The choice of material is one of the significant contributors to the total cost. For instance, timber walls are typically cheaper than concrete or stone walls but may lack longevity.
- Timber: $15-$25 per square foot
- Interlocking concrete blocks: $20-$30 per square foot
- Natural stone/ boulder walls: $25-$40 per square foot
- Poured concrete/ brick: $30-$40 per square foot
These prices vary based on factors like quality and source location. It’s essential to factor in additional costs like delivery charges or equipment rental for heavier materials.
Labor Costs
Labor costs can be as variable as material costs based on factors like terrain complexity and wall height. The average rates range from $50 to $60 per hour for labor alone. With skilled labor being costly, it becomes essential to accurately estimate the project duration to avoid budget overruns.
Design and Planning Costs
A retaining wall’s design can significantly influence its cost. A simple straight wall will generally be less expensive than curved or tiered walls due to increased complexity and required materials. Typically, professional design fees range between 15% – 20% of your total project cost.
Permits and Inspections
While not directly linked to construction, permits and inspection fees contribute towards overall costs. These amounts vary from region to region but can range anywhere from $50 – $500+.
Maintenance and Repair
Although not an upfront cost, maintenance and repair should also be considered when budgeting. Timber walls, for instance, require regular treatments to prevent rot and insect damage that can add recurring costs.
In summary, the cost of building a retaining wall is influenced by several factors. While this provides a general idea of potential expenses, it’s important to seek specific local quotes to ensure accurate budgeting. Moreover, it’s worth investing in high-quality materials and professional labor to ensure the longevity of your retaining wall, which can save on long-term maintenance costs.
Tags: