Predicting the Financial Implications: Concrete Costs in 2025
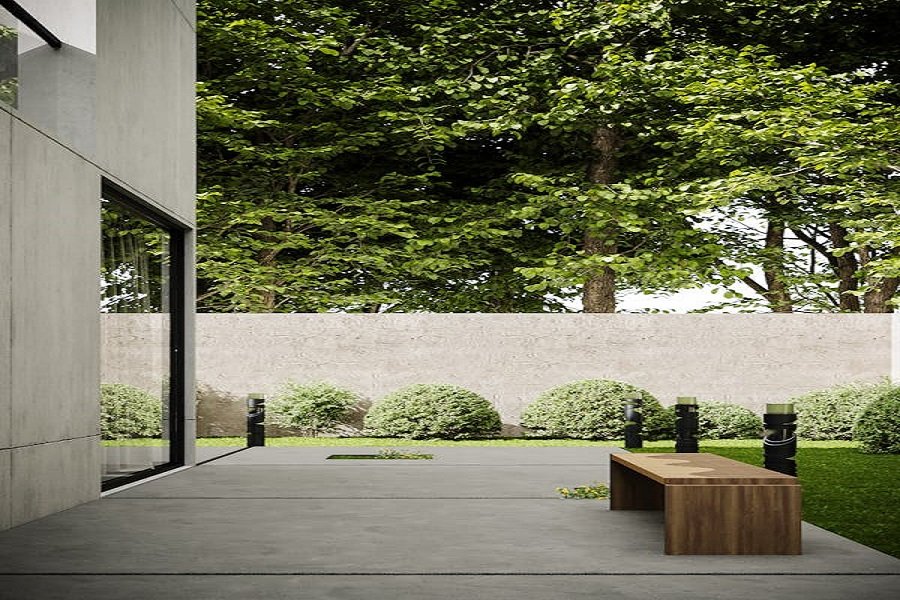
Concrete Cost
Concrete is an essential material in many construction projects, and its cost significantly impacts the overall project budget. Predicting the financial implications of concrete costs can be a challenging task due to various factors influencing its price. However, by analyzing market trends, economic indicators, and industry advancements, one can make educated predictions about concrete costs in 2025.
Market Trends
- The rise in urbanization and infrastructural developments worldwide increases the demand for concrete.
- Innovations in manufacturing processes, such as the use of recycled materials and energy-efficient techniques, are likely to reduce production costs.
Based on these market trends, it’s expected that the demand for concrete will continue to rise until 2025.
Economic Indicators
- Inflation rates: High inflation rates can increase material costs due to rising production expenses.
- Interest rates: Higher interest rates discourage borrowing for construction activities, which may lead to a decrease in demand for concrete.
- GDP growth: A robust GDP growth rate signifies economic prosperity that could potentially lead to increased infrastructure investments and high demand for concrete.
Considering current economic projections, expect moderate fluctuations in the price of concrete through 2025.
Technological Advancements
- Use of artificial intelligence (AI) and automation: These technologies streamline production processes reducing operational costs which might reflect on end-product prices.
- Development of new types of concretes like self-healing and translucent ones: These innovations might initially increase product cost due to R&D expenses but would decrease over time as they mature.
While technology tends to reduce production costs, the adoption of advanced concrete types may initially push prices up before they stabilize.
Supply-Demand Equilibrium
The principle of supply and demand applies to concrete as well. If the concrete supply exceeds demand, prices are likely to decrease. Conversely, if demand surpasses supply, expect an increase in cost.
Based on population growth trends, urbanization rates, and infrastructural development plans across various countries, the demand for concrete is projected to remain high until 2025.
In conclusion, anticipating concrete costs in 2025 involves examining market trends, economic indicators, technological advancements and supply-demand dynamics. Although precise forecasts are challenging due to variable factors, one can expect moderate fluctuations with an overall upward trend until 2025 given current projections. This information should help stakeholders in construction projects plan their budgets more accurately and efficiently.
Understanding the Cost Variation: A Comprehensive Guide on Concrete Expenses
Understanding the cost variation in concrete expenses is crucial for any construction project. The cost of concrete is affected by multiple factors, such as the market price for raw materials, labour charges, transportation fees and more. This comprehensive guide will provide a detailed insight into these elements and aid in a deeper understanding of concrete costs.
Factors Influencing Concrete Costs
- Material Costs: Concrete mainly consists of cement, aggregate (like sand or gravel), and water. The prices of these materials can vary based on their availability and market conditions.
- Labour Costs: Labour costs can fluctuate depending on the region, complexity of work, and current demand for construction work.
- Delivery Charges: These depend on the distance between the concrete production plant and construction site. Greater distance means higher transportation costs.
It’s important to note that although these are the basic factors that influence the cost of concrete, there may be other variables that come into play depending upon specific projects or locations.
Price Variation Based on Concrete Types
- Ready-Mix Concrete: It’s prepared at a central plant according to specific mix designs suiting project requirements. On average, it can cost around $115-$150 per cubic yard.
- High Strength Concrete: Designed for constructions requiring higher strength like commercial buildings or heavy-duty roads. Its cost varies from $135-$180 per cubic yard.
- Decorative Concrete: Used for aesthetic purposes like patios or driveways with added colors or textures. This type can range from $100-$150 per square foot depending upon design intricacy.
Keep in mind these prices are just averages and can vary greatly based on your location and supplier.
Concrete Cost Versus Other Construction Materials
When comparing the cost of concrete with other construction materials like brick, wood, or steel, it is important to consider the durability, maintenance cost and lifecycle of these materials. While concrete might have a higher initial cost than some materials, its long-term durability and low maintenance requirements often make it a more economical choice in the long run.
In conclusion, understanding the cost variation in concrete can help you better plan your construction budget. By taking into account all possible factors that influence the cost of concrete, you can make informed decisions that will result in efficient utilization of resources and successful project execution.
How to Efficiently Estimate Concrete Cost Based on Project Size
When it comes to construction projects, one of the most frequently used materials is concrete. Its versatility and durability make it an ideal choice for various construction applications, from residential buildings to expansive commercial structures. However, accurately estimating the cost of concrete based on project size can sometimes be a challenging task. This article aims to provide some useful tips on how to do this efficiently.
Start with Simple Calculations
The first step in estimating the concrete cost for your project is determining how much concrete you need. This can usually be done by calculating the volume of your project area (in cubic yards) and then multiplying it by the average cost per cubic yard of concrete.
- Measure your project area: length x width x depth (all in feet)
- Convert that measurement into cubic yards: [total measurement in feet] / 27
- Multiply by average cost per yard
The average price for a yard of concrete ranges between $75 to $125, but prices can fluctuate based on location, supplier, and current market conditions.
Type of Concrete Matters
Not all concrete is created equal; different types have varying costs. Standard ready-mix concrete is typically the least expensive option, while specialized mixes (like high-strength or decorative concrete) can cost more due to their unique properties and additional ingredients.
Therefore, incorporate the type of concrete you plan on using into your calculations. Research prices from different suppliers before settling on a particular one.
Consider Labor Costs
Aside from material costs, you also need to factor in labor costs into your calculations. The complexity of your project will dictate these expenses – simple patio pours will cost less than intricate foundation work involving reinforcements and complex forms.
Remember that labor costs are typically billed hourly and include site preparation, form setup and removal, pouring and finishing. Depending on how intricate or large-scale your project is, these costs can significantly influence your overall concrete expenditure.
Don’t Forget the Extras
- Delivery Fees: If your project requires a significant amount of concrete, you may need to have it delivered, which will incur an extra cost.
- Pumping Fees: Some projects may require the use of a concrete pump, which can add to your total cost.
- Expedited Service Fees: If you need quick or after-hours delivery, expect additional charges.
Remember, every project is unique and so are its potential costs. It’s crucial to conduct a thorough assessment of your specific construction needs before starting any work or purchasing materials. This way, you’ll have an accurate estimate of your project’s total concrete cost beforehand and avoid unpleasant financial surprises down the line.
Deducing Your Requirements: Calculating Cubic Yard of Concrete for Your Project
Estimating the needed quantity of concrete for a project is an important task that directly affects the overall cost and completion time. The most common way to measure concrete is in cubic yards. If you’re handling a construction project, it’s crucial to accurately calculate how many cubic yards of concrete you will need.
Understanding the Concept of Cubic Yards
A cubic yard is a unit of volume used in the United States customary and imperial systems of measurement. It’s defined as the volume of a cube with sides measuring one yard (3 feet or 0.9144 meters) on each side. In concrete projects, this measurement helps determine the amount of material required.
Basic Calculation for Cubic Yards
- Measure the area where the concrete will be placed by length, width, and depth in feet.
- Multiply these three measurements together to find the total cubic feet.
- Convert this figure into cubic yards by dividing by 27 (since there are 27 cubic feet in one cubic yard).
- Convert depth from inches to feet: 4 inches = 0.33 feet
- Calculate total cubic feet: 12 * 8 * 0.33 = ~32 ft³
- Convert to cubic yards: ~32/27 = ~1.19 yd³
So, around 1.2 cubic yards of concrete would be required for this project.
Adjusting For Waste and Overages
When ordering concrete, it’s always wise to add a bit more than what your calculations show you’ll need. This allows for waste or overage due to variance in measurements or unexpected project conditions. A common rule of thumb is to add 10-20% to your calculated volume.
The Role of Concrete Calculator Tools
For more complex projects, consider using online concrete calculators. These tools can simplify the process, especially when dealing with irregular shapes, multiple sections, or more complex depth variations.
By accurately evaluating your project’s concrete requirements in cubic yards, you can ensure a more cost-effective and efficient construction process. Maintaining precision in these calculations is crucial to avoid unnecessary expenses or delays in project timelines. Therefore, understanding how to calculate the amount of concrete needed for a project is an essential skill in construction and project management.
The Hidden Contributors: Other Factors That Affect the Overall Concrete Cost
While the basic price of concrete and the cubic yard requirements for a project are key considerations in estimating the total cost, they are not the only factors. Several hidden contributors can significantly alter the final concrete cost. Gaining awareness of these factors is critical to budgeting accurately and effectively managing your resources.
Weather Conditions
- Hot weather often requires retarders to slow down the hydration process.
- Cold weather, on the other hand, may call for accelerators to speed up hydration or heaters to prevent freezing.
These extra materials increase costs and need to be factored in when estimating total project expenses.
Complexity of Project
The complexity of a project significantly affects its cost. If your project involves intricate designs, difficult-to-reach areas, or complex forms, it will likely require more labor and could take longer than a straightforward job. This increases both labor costs and time spent on site – all contributing to overall expenditure.
Quality of Subgrade
The quality of the subgrade – the ground on which concrete is poured – can directly affect overall costs. If your subgrade is uneven or unstable, you may need additional work like grading or compacting before pouring concrete. This additional preparation comes at an extra cost and should be considered when budgeting for your project.
Distance from Supplier
Logistical factors can also impact overall concrete expense. The further away your job site is from your supplier, the higher transport fees will be due to increased fuel consumption and driver time. It’s essential to consider these potential costs when planning your budget.
Labor Costs
Finally, labor expenses account for a significant portion of any concrete project’s overall cost. Labor rates vary based on market conditions, the skill level of workers, and regional standards. In addition, time-consuming tasks like setting up and removing forms or finishing the concrete surface add to labor costs.
Understanding these hidden factors will lead to more accurate budgeting for your concrete project. Therefore, in addition to calculating concrete volume needs and understanding basic material costs, consider weather conditions, project complexity, subgrade quality, distance from supplier, and prevailing labor rates when planning your budget. Doing so will help avoid unwanted surprises and ensure that your project stays on track financially.
Strategizing Project Logistics: The Impact of Delivery Day and Distance on Concrete Cost
When it comes to the cost of concrete, it’s not just about the material’s price per cubic yard. There are many other factors to consider, including delivery logistics. The day of the week that the concrete is delivered and the distance it has to travel can significantly impact your overall costs.
Impact of Delivery Day on Concrete Cost
The delivery day can play a crucial role in determining the overall cost of your concrete project. While most suppliers operate Monday to Saturday, there can be variation in pricing based on demand and operating hours.
- Weekdays: Deliveries during weekdays are often more cost-effective as this is a standard operating time for most suppliers. However, during peak construction season, weekdays can be busier which could lead to scheduling challenges.
- Weekends: Some suppliers may charge higher rates for weekend deliveries due to increased operating costs or lower availability. If you have flexibility with your schedule, you might want to avoid weekend deliveries to cut down on costs.
- Holidays: Similar to weekends, holiday deliveries can come with a premium price tag due to limited operations or increased demand.
Effect of Delivery Distance on Concrete Cost
- Travel Time: Suppliers usually charge a fee based on the travel time from their plant or warehouse to your site. This is because longer distances mean more fuel consumption and increased wear and tear on their vehicles.
- Delivery Quantity: For long-distance deliveries, suppliers often require a minimum order quantity. If your project doesn’t need that much concrete, you may end up paying for more than you require just to meet this minimum.
Strategies for Minimizing Delivery Cost
- Schedule Wisely: To save money, try to schedule your concrete delivery for a weekday when rates are often lower and availability is typically higher.
- Choose Local Suppliers: Opting for a local supplier can also reduce travel time and cost. Plus, you’re more likely to receive timely service in case of any last-minute changes or emergencies.
- Consolidate Orders: If possible, try to consolidate orders with neighboring projects. This approach allows you to share the minimum quantity, reducing the overall cost.
- Calculate Accurately: Ensure you calculate your concrete needs accurately to avoid over-ordering or under-ordering, both of which can increase costs significantly.
By understanding how delivery day and distance factor into your concrete costs, you can make smarter decisions about project planning and potentially save on overall expenses.
Master Strategies for Effective Site Preparation Prior to Concrete Installation
Proper site preparation is a critical step in any concrete installation project. It’s not only about ensuring a stable and level base for the concrete, it also involves mitigating potential risks that could compromise the quality and durability of the completed project. Here, we outline several master strategies that can lead to effective site preparation prior to concrete installation.
Planning and Designing
Firstly, it’s crucial to have a comprehensive plan and design of the project you’re undertaking. This assists in identifying potential challenges so necessary measures can be put in place. Consider variables like the proximity of utilities, environmental factors like drainage or soil type, and local regulations or permits needed.
Site Clearing
Site clearing involves removing obstructions such as vegetation, debris, or pre-existing structures from the site where concrete will be installed. This step is essential for preventing future structural problems caused by organic materials decomposing underneath the slab.
Ground Compaction to Ensure Stability
The stability of a concrete slab largely depends on ground compaction. Whether done manually or using mechanical compactors, ensure that the ground is compacted uniformly to enhance stability and prevent future settlement problems.
Installing Drainage Systems
Poor drainage can cause numerous problems for concrete structures such as cracking or buckling due to water pressure build-up. Therefore, before installing your concrete slab, ensure adequate drainage systems are in place. Your approach might involve grading the site properly so water naturally drains away from your structure.
Setting up Formwork
Formwork is used to hold wet concrete in place until it hardens into its desired shape. The formwork should be set up accurately according to your design plans and adequately secured to prevent shifting during pouring.
Preparing Base Material
Base material provides additional support for your concrete slab. Typically made from crushed stone or gravel, this layer should be evenly graded and compacted before pouring the cement.
Reinforcement Installation
If your project calls for reinforced concrete, installation of the reinforcement material (like rebar or wire mesh) comes next. This is usually tied together and placed within the formwork before the concrete is poured, providing added strength and durability to the final structure.
Ordering and Scheduling Concrete Delivery
Finally, once your site is prepared, it’s time to order and schedule your concrete delivery. Work closely with your supplier to ensure you have the correct amount and mix of concrete delivered at the right time.
Thorough site preparation can help reduce future maintenance costs, prevent structural issues, and ensure a long-lasting, high-quality concrete installation. By following these strategies for effective site preparation prior to concrete installation, you can lay the groundwork for a successful project.
Tags: